CRIL Tech’s Third Webinar Recap: From Prototype to Production
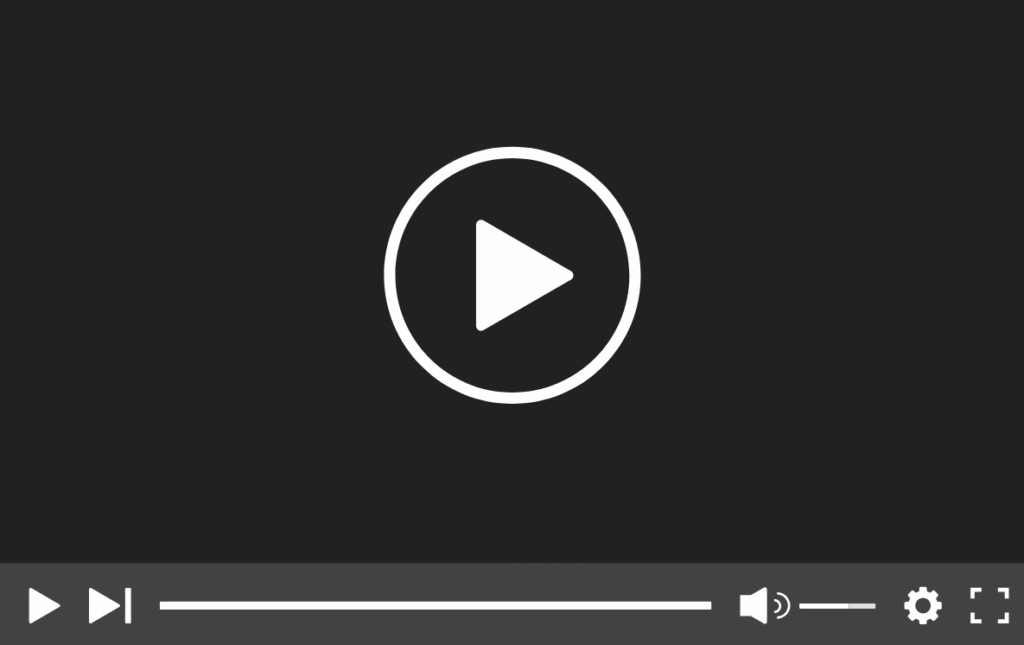
We are thrilled to share highlights from our third webinar – and the second in CRIL Tech’s focused expert series – designed to equip medical device companies with the insights and tools needed to navigate the journey from concept to scalable manufacturing. This session brought together experts from Israel and Costa Rica to discuss real-world strategies, common pitfalls, and key considerations for scaling production in today’s dynamic global trade environment. Watch the full webinar recording here 🛠️ What We Covered Bridging the Gap: From Prototype to ScaleOhad Kazoom, co-founder of CRIL Tech, opened the session by sharing practical advice on the critical transition from early-stage prototyping to full-scale production. He highlighted common challenges faced by startups and growing companies, such as maintaining quality while increasing volume, and offered actionable solutions for overcoming them. Vertically Integrated Manufacturing: A Supplier’s PerspectiveRommy Huleis of Cadence provided valuable insights into how vertically integrated contract manufacturing can accelerate production timelines, reduce costs, and improve quality. Drawing on Cadence’s experience serving global MedTech companies, Rommy showcased how a single supplier can support projects from design to finished product. Silicone Solutions: End-to-End ExpertiseOded Stein of Silicone Value presented a deep dive into silicone manufacturing solutions, focusing on how their comprehensive approach—from design through production—helps clients achieve regulatory compliance and production efficiency. Oded also shared success stories of companies that scaled effectively using Silicone Value’s expertise. 💡 Key Takeaways Attendees gained a wealth of practical insights, including: How to avoid common scaling pitfalls in MedTech manufacturing. The benefits of working with vertically integrated suppliers. Why Costa Rica’s ecosystem, supported by companies like Cadence and Silicone Value, offers a competitive advantage for companies targeting the U.S. market. The interactive Q&A session addressed pressing questions from participants, covering topics such as regulatory considerations, supply chain risks, and strategies for achieving faster time-to-market. 🎥 Missed the Webinar? No problem! You can watch the full recording [here]. 📢 What’s Next? Our expert series continues to deliver high-value content for companies seeking smarter manufacturing solutions. Follow CRIL Tech on LinkedIn and subscribe to our newsletter to stay informed about upcoming webinars and industry insights.
Costa Rica’s Aerospace and Defense Industry: A Rising Hub for Precision Metal Manufacturing
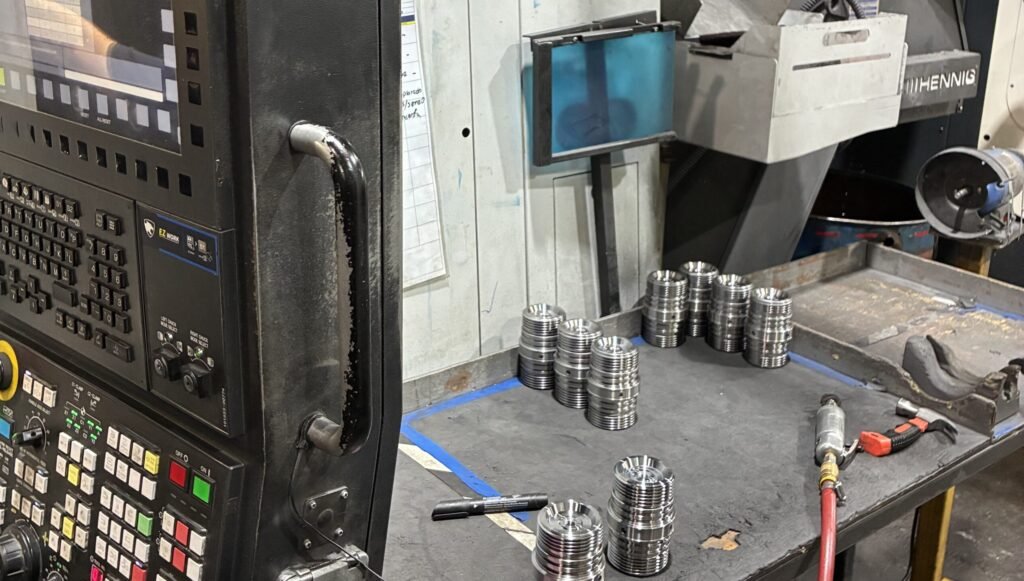
Costa Rica has quietly emerged as a high-performance hub for precision metal manufacturing and advanced machinery. With decades of experience in CNC machining, metal fabrication, and complex part production, the country has become a reliable source for high-spec components used in aerospace, defense, and other demanding industries. This strength is reflected in the Costa Rica Aerospace Cluster—home to over 40 companies offering everything from precision machining and electromechanical assembly to software testing and MRO services. Supported by a stable economy and a skilled industrial workforce, these companies now export high-value products globally, supplying major manufacturers across the United States, Europe, and Latin America. TECHSHOP Machinery and Parts Certified Quality, Global Standards Quality and compliance are at the core of Costa Rica’s industrial development. Many manufacturers in the country meet international aerospace and defense requirements, including certifications like AS9100D, NADCAP, and ISO 9001. These standards ensure consistent reliability, process control, and traceability—critical for any organization sourcing critical parts or assemblies. A standout example is Techshop International, a Costa Rican precision machining company established in 1980. Techshop holds AS9100D/ISO 9001 certifications and delivers highly accurate machined components for aerospace, defense, and industrial clients. Its proven track record and local engineering expertise reflect the broader capabilities available in the Costa Rican ecosystem. Why Costa Rica? Key Advantages for Manufacturers and Buyers Costa Rica offers a compelling mix of technical capability, cost-efficiency, and operational stability. For companies in Israel and around the world seeking alternatives to congested or expensive supply chains, it represents a powerful nearshore solution. Among its strategic advantages: Skilled Workforce – The country ranks #1 in Latin America for human capital in engineering and technical fields, supported by strong public education and vocational training. Economic and Political Stability – Costa Rica has a long-standing democratic tradition, low corruption, and strong legal protections for intellectual property. Quality-Focused Culture – The steady growth in aerospace certifications is a sign of an ingrained commitment to quality and continuous improvement. Trade Access – With free trade agreements covering much of the Americas and Europe, manufacturers in Costa Rica can deliver products quickly and competitively. Responsive, Agile Production – The country’s industrial sector is known for flexibility and client-focused service—an important asset in today’s unpredictable supply chain environment. CRIL TECH: Bridging Israeli Needs with Costa Rican Precision At CRIL Tech, we are actively involved in Costa Rica’s growing aerospace and defense ecosystem. We work closely with several vetted manufacturers—some of which we represent exclusively in Israel—to provide high-quality components and supply solutions for Israeli and international clients. We believe Costa Rica is an ideal sourcing and manufacturing destination, especially for companies seeking reliable alternatives to traditional supply routes. Whether it’s CNC-machined parts, electromechanical assemblies, or full nearshoring solutions for the U.S. and Latin American markets, our partners in Costa Rica deliver world-class quality at highly competitive prices. Our team operates both in Israel and on the ground in Costa Rica, ensuring fast, responsive service. We physically visit production sites, conduct real-time quality checks, and oversee manufacturing processes from start to finish. This hands-on local presence means issues are solved quickly, quality is maintained, and clients receive exactly what they need—on time and on spec. If you’re looking to strengthen your supply chain, reduce production delays, or explore strategic sourcing opportunities, we invite you to leave your contact information. A member of our team will get back to you promptly to discuss how Costa Rica—and CRIL Tech—can support your next move.
CRIL Tech’s Second Webinar Recap: Deep Dive into Nearshore Manufacturing
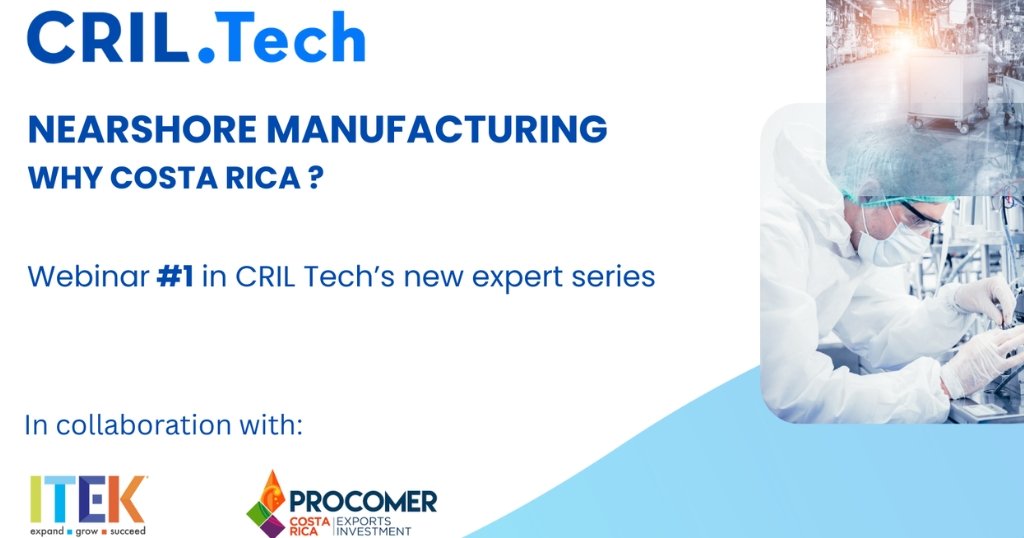
We are pleased to share a recap of our latest webinar, which explored nearshore medical device manufacturing strategies specifically for medical device companies. This session provided a focused look at Costa Rica’s unique advantages as a nearshore destination, featuring insights from both government bodies and industry leaders. It is a continuation of our first webinar, which delved into Costa Rica’s thriving medical device industry. Click here to watch the webinar So What We Covered: Understanding Nearshore Manufacturing: tamar Cohen, co-founder and CEO of CRIL Tech, opened the session by explaining the concept of nearshoring—manufacturing closer to your target market rather than in distant locations like Asia. He compared major nearshore destinations (Mexico, the Dominican Republic, and Costa Rica), highlighting why Costa Rica stands out as the optimal choice for companies targeting the U.S. market. Itamar concluded his segment by outlining CRIL Tech’s services: helping companies establish operations in Costa Rica through trusted local partners, handling everything from compliance to logistics. Costa Rica’s Advanced Manufacturing Ecosystem: Marcela Salazar Leitón, Specialist in Advanced Manufacturing at PROCOMER, gave a comprehensive presentation on Costa Rica’s manufacturing landscape. (PROCOMER is Costa Rica’s official government agency for export and investment promotion.) Marcela detailed the impressive growth of Costa Rica’s medical device sector, the presence of global leaders like Medtronic and Johnson & Johnson, and the robust support offered by the Costa Rican government. She also emphasized the country’s political and economic stability, the benefits of Free Trade Zones, and the full suite of services PROCOMER provides to companies investing in Costa Rica. A Manufacturer’s Perspective: Bernal Rodríguez Jiménez, CEO and founder of ITEK, provided a unique insider’s view. Bernal shared his perspective as a 100% Costa Rican manufacturer focused on nearshore production for U.S. clients. He discussed ITEK’s growth story, its full capabilities (from clean room production to stringent quality control), and Bernal also highlighted success stories of international clients who have benefited from ITEK’s end-to-end solutions. ITEK is a close partner of CRIL Tech and is represented exclusively by CRIL Tech in the Israeli market. Key Takeaways: Attendees gained actionable knowledge on: The tangible benefits of nearshoring for medical device companies. Why Costa Rica’s integrated ecosystem offers a competitive edge. Real-world case studies and regulatory insights that de-risk manufacturing investments. At the end of the session, Amir Rokman, Deputy Chief of Mission and Economic Attaché at the Embassy of Israel in Costa Rica, joined the webinar to express his strong support for CRIL Tech’s activities and to highlight the Embassy’s ongoing role in strengthening commercial ties between Israel and Costa Rica. Looking Ahead: This CRIL Tech webinar is part of our ongoing effort to provide expert insights and practical guidance for companies exploring nearshore manufacturing solutions. Our webinar series is designed to provide continuous value as global manufacturing evolves. Stay tuned for upcoming sessions by following CRIL Tech on LinkedIn and subscribing to our newsletter. Missed This Webinar? Click here to watch the recording
IQ, OQ, PQ: Three Critical Stages in Scaling Up to Full Production
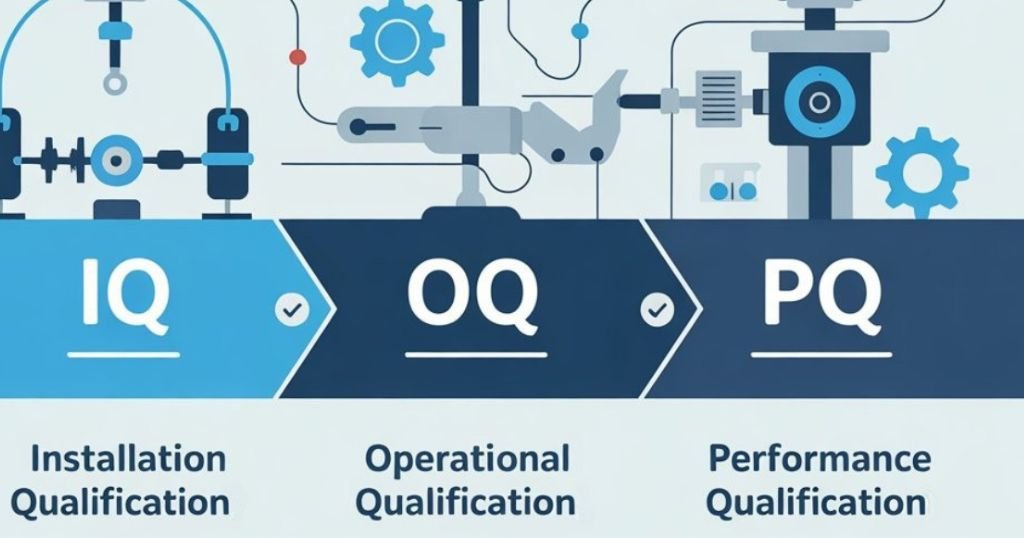
When a medical device company transitions from development and prototyping to full scale manufacturing, one of the most critical challenges is ensuring that all processes, equipment, and systems are ready to deliver consistent, safe, and high quality products. At this stage, the three core validation stages IQ, OQ, and PQ, become essential tools. These stages act as structured checkpoints not only for confirming compliance with regulations from authorities like the FDA, but also for minimizing risk, improving efficiency, and ensuring the final product meets all specifications. What Are IQ, OQ, PQ and Why Are They Important in Scaling Production? While IQ, OQ, and PQ are essential whenever new equipment or processes are introduced, they become especially important during scale-up. This phase often involves transitioning from R&D or pilot batches into full production, where validation ensures that the infrastructure is ready to meet regulatory expectations and production goals. During the shift from pilot-scale production to commercial manufacturing, companies must ensure that every part of the production line functions properly, from the installation of equipment to its long term, consistent performance. The IQ/OQ/PQ process provides a structured framework to verify that equipment is installed correctly (IQ), operates as intended (OQ), and consistently performs under real manufacturing conditions (PQ). Each phase builds confidence in the manufacturing process and is crucial for regulatory compliance, internal quality assurance, and long-term operational success. IQ – Installation Qualification IQ is the foundation of the validation process. It confirms that all manufacturing equipment and systems are installed according to design specifications, manufacturer requirements, and regulatory standards. This phase typically includes: Verifying that equipment is located and anchored correctly per the approved layout Confirming all utility connections (e.g., electricity, compressed air, vacuum, water) are properly installed and operational Checking that installation follows cGMP standards and complies with safety and environmental requirements Ensuring all components and materials are correct, complete, and documented Reviewing calibration certificates for instruments, gauges, sensors, and control systems Example: Installing a new cleanroom filling machine and confirming that all connections – electrical, air, and water – are properly made, materials meet cleanroom standards, and documentation is complete. What does IQ verify? IQ verifies the Design Specification – ensuring the system was built and installed as planned. OQ – Operational Qualification OQ focuses on verifying that the equipment and systems operate as expected within predefined operating ranges. It evaluates functionality, safety features, and control capabilities. This phase typically includes: Running equipment at minimum, nominal, and maximum settings to verify reliable performance Validating critical alarms, interlocks, and emergency shutdown systems Simulating fault conditions to assess system responses Confirming automation and control logic (PLCs, HMIs) operate correctly Documenting all test results and deviations Example: Running a packaging machine at different speeds to confirm seal temperature stability, testing alarms and interlocks, and ensuring it stops properly during a fault condition. What does OQ verify? OQ verifies the Functional Specification – confirming the system functions safely and reliably. PQ – Performance Qualification PQ is the final validation stage. It verifies that the equipment consistently produces products that meet quality specifications under actual production conditions. This phase typically includes: Running multiple full-scale production batches (typically three) under routine conditions Sampling and testing finished products for critical quality attributes (CQA) Conducting statistical analysis (e.g., Cpk, PpK) Verifying documentation traceability and batch record completeness Example: Producing three full batches of medical tubing under standard production conditions and confirming that all dimensional, mechanical, and visual specifications are consistently met. What does PQ verify? PQ verifies the User Requirements Specification – proving that the system meets the real world needs of the user. The System Validation Journey CRIL Tech Support At CRIL, we specialize in helping companies scale from early-stage production to full scale manufacturing. Whether setting up new production lines or validating new processes, we work closely with our clients to ensure each step is completed accurately and efficiently – IQ, OQ, or PQ We closely monitor the entire validation journey, from installation to performance runs, ensuring that every requirement is met and documented. Our team works side by side with production, engineering, and quality personnel to address technical issues, streamline testing, and meet regulatory expectations without delays. Our goal is to give our clients peace of mind during the scale up phase – delivering robust validation processes that ensure readiness for commercial success. Planning to launch a new medical device production line? Let’s talk about how CRIL can help you get there.
Understanding Nearshore Manufacturing
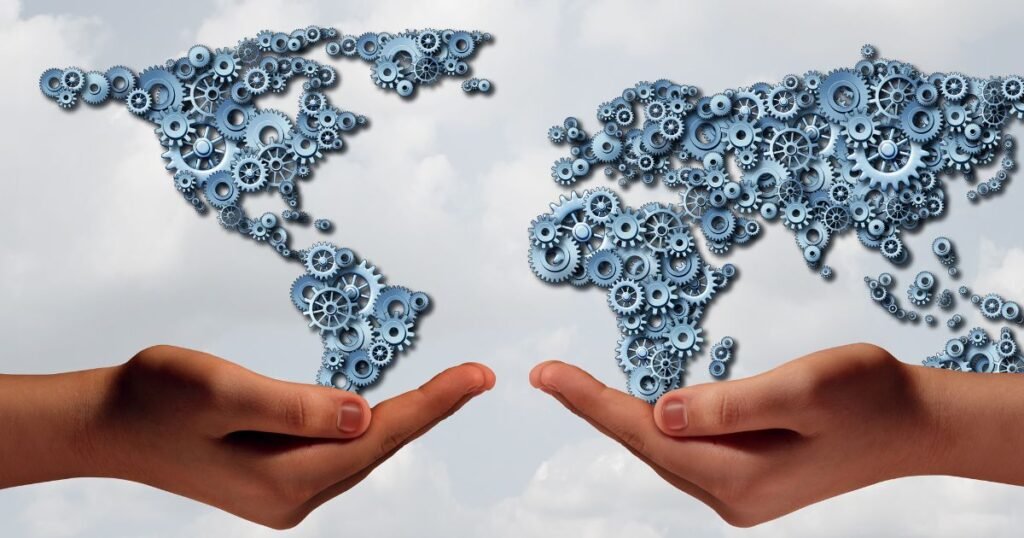
In today’s global market, companies are constantly looking for ways to stabilize their operations, improve efficiency, and stay competitive. One strategy gaining momentum is nearshore manufacturing – producing goods closer to the target market instead of relying on distant offshore locations. But why are so many companies making the shift? What is Nearshore Manufacturing?Unlike offshore production (e.g., U.S. companies manufacturing in China or India), nearshoring is the concept of relocating production closer to the company’s interests. For companies targeting the U.S. market, this often means Central America or the Caribbean. The idea is simple: achieve lower costs without the risks of long supply chains, delays, and communication barriers. Why is Nearshoring on the Rise? Recent global disruptions have highlighted the weaknesses of long supply chains. Events like the COVID-19 pandemic and the Suez Canal blockage exposed the risks of relying on faraway production hubs. Nearshoring solves these challenges by offering: Faster delivery & fewer supply chain risks streamline operations and responsiveness to market demands Cost-efficient manufacturing with reduced logistical expenses Easier compliance with U.S. regulations and quality Real-time communication & faster decision-making Costa Rica: A Nearshoring Success Story Some countries have strategically developed nearshore industries to serve major markets more efficiently. Costa Rica is a great example, having built a strong and rapidly growing medical device manufacturing sector that meets U.S. quality standards. In 2023, Costa Rica exported over $8.3 billion worth of products to the U.S., with medical devices making up $5 billion of that total. The medical device sector alone has grown by more than 15% annually since 2014, reflecting the country’s increasing prominence in the global market. Its proximity to the U.S., stable political environment, and attractive tax incentives have made it a top destination for major U.S. manufacturers like Abbott, Medtronic, and Johnson & Johnson, all of which have established production facilities in it. Additionally, Costa Rica benefits from the CAFTA-DR free trade agreement, allowing duty-free exports to the U.S. Is Nearshoring Right for Your Business? For companies looking to expand, cut costs, or improve supply chain resilience, nearshoring is a game-changer. At CRIL Tech, we specialize in helping businesses transition to cost-effective, high-quality nearshore manufacturing. Let us guide you through the process and unlock the full potential of nearshoring. Learn more about our Costa Rica manufacturing solutions
Costa Rica’s Industry – A Gateway to Advanced Manufacturing Excellence
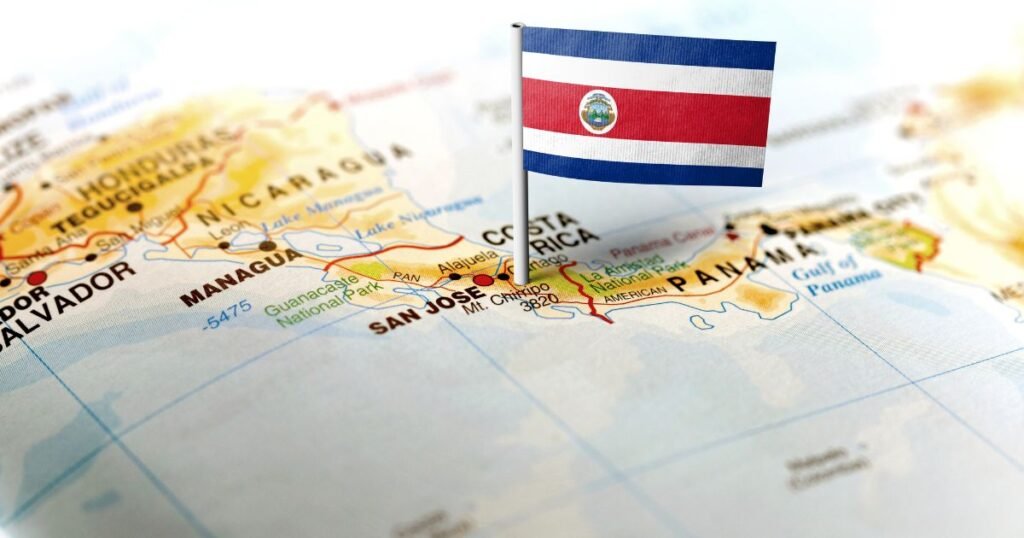
Costa Rica has cemented its position as a global leader in advanced manufacturing, particularly in the medical device industry. This remarkable transformation is the result of forward-thinking policies, a commitment to quality, and a strategic location that places Costa Rica at the crossroads of global trade. Over the past decade, the country has become a preferred destination for companies seeking cost-effective, high-quality, and efficient manufacturing solutions. Today, it is home to over 80 multinational medtech companies, including industry giants such as Medtronic, Abbott, and Boston Scientific. The success of Costa Rica’s manufacturing sector is underpinned by several key factors. First and foremost are the Free Trade Zones (FTZ), which provide unparalleled benefits for businesses. These zones offer exemptions on corporate taxes, import duties, and other levies, significantly reducing production costs. Additionally, the FTZs are strategically located near major ports and airports, ensuring seamless logistics and access to key markets. This has helped Costa Rica achieve consistent growth in its exports, with medical device exports alone reaching $7.4 billion in 2023—a 342% increase since 2014. Another cornerstone of Costa Rica’s success is its highly skilled workforce. The country places a strong emphasis on STEM education, ensuring a steady supply of technically proficient workers adept at handling complex manufacturing processes. This has allowed Costa Rica to transition from producing basic medical disposables to high-tech devices such as surgical instruments, diagnostic equipment, and therapeutic implants. The combination of a skilled workforce and advanced manufacturing capabilities ensures that companies operating in Costa Rica can maintain the highest standards of quality. Costa Rica’s strategic location further enhances its appeal. Situated at the heart of the Americas, the country offers proximity to the United States, its largest trading partner, which enables faster shipping times and reduced transportation costs. This advantage is particularly valuable for industries that rely on timely delivery, such as medical devices. Coupled with its stable political and economic environment, Costa Rica provides a secure and efficient base for global manufacturing operations. For businesses exploring opportunities in Costa Rica, it’s important to have local expertise to navigate the complexities of the market. While the country offers immense potential, understanding its regulatory environment, supplier network, and logistical infrastructure is key to unlocking its full value. At CRIL Tech, we specialize in helping companies seamlessly integrate into Costa Rica’s advanced manufacturing ecosystem. With a local Israeli team on the ground, we provide real-time support, ensuring smooth operations and minimizing risks. From identifying the right suppliers to managing production processes, CRIL Tech is your trusted partner in making Costa Rica work for you. Costa Rica’s medical device industry exemplifies what’s possible when innovation, strategic policies, and a commitment to quality converge. As the country continues to grow and diversify its manufacturing capabilities, it remains an unparalleled destination for businesses looking to optimize production and expand into global markets. By choosing Costa Rica, you’re not just choosing a manufacturing base—you’re choosing a partner for success. Learn more about our Costa Rica manufacturing solutions
CRIL Tech’s First Webinar Recap
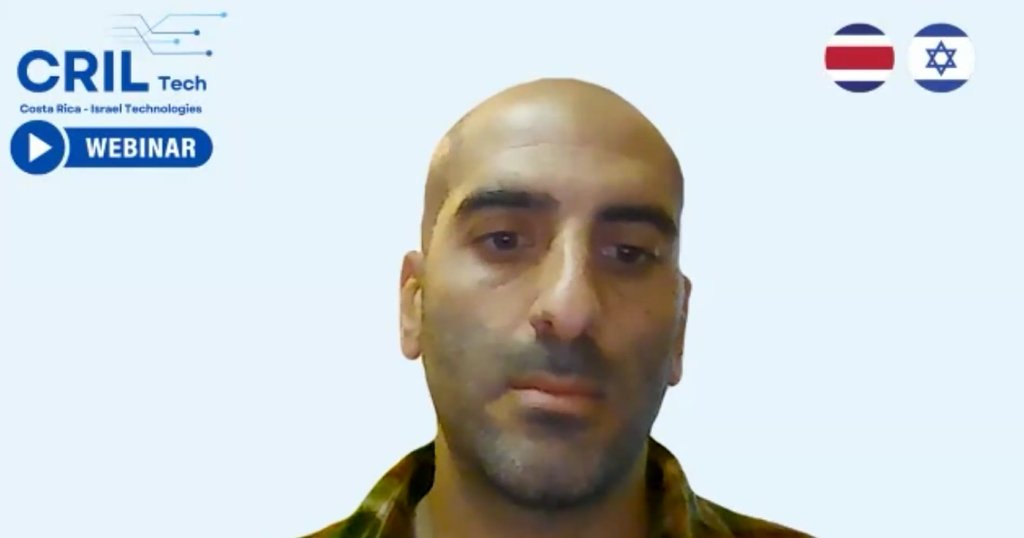
CRIL Tech had the pleasure of hosting our inaugural webinar, marking a significant milestone in our mission to connect Israeli companies with Costa Rica’s thriving manufacturing ecosystem. Partnering with PROCOMER, the Embassy of Israel in Costa Rica, and PRMC, we brought together industry leaders and experts to shed light on how Costa Rica’s advanced manufacturing can drive innovation, efficiency, and cost savings for Israeli businesses. Click here to watch the webinar What We Covered: Key Takeaways for Participants:The webinar wasn’t just about presentations; it was an interactive session where attendees asked crucial questions, such as: Participants walked away with a clear understanding of: Missed the Webinar?Don’t worry! You can watch the full recording here. What’s Next?We’re thrilled with the success of our first webinar and are already planning our next event. Follow us on LinkedIn and subscribe to our newsletter for updates on upcoming webinars and exclusive content. Conclusion:Our December webinar was more than just a discussion – it was an opportunity to connect, learn, and explore the endless possibilities of manufacturing in Costa Rica. Join us in shaping the future of production!